Digitize, Digitalize, Automate – and what’s the difference?
Digitize, Digitalize, Automate
Everyone – like me – loves a good buzzword, and just like three letter acronyms they exist right throughout the business. To avoid confusion, here is a simple way of thinking about digitization, digitalization and automation without adding to the confusion. Let’s think about this with my example: Renewing your driving licence.
Digitize – 2 dimensional
Suppose you complete an inspection or run sheet on paper and then scan it to produce a PDF. This is digitizing the information. It helps to minimize physical storage space, or the need to transfer the information in an analogue way, but that is about it.
So, for our example of renewing your licence, you pick up the renewal form from the post office and fill it out with a pen, scan it and email it to the transport department. You have digitized the information.
Digitalize – 3 dimensional
Rather than completing a form on paper, you now use an app to enter the data directly into a handheld device, like a tablet or smartphone. The information is now captured and useable without further manipulation. In this context, digitalization allows the smart capture, transmission, approval, processing and use of information.
The transport department have updated their website, so now you can complete your licence application form online. The information is collected, processed and used directly through a single portal. The information has been digitalized.
Automate – 4 dimensional
Forms? No longer needed. Automation involves setting processes in place which occur in the background, without human intervention. Logic is programmed and applied allowing the system to control the output, knowing the inputs. The process is triggered by time, or by an event – the fourth dimension!
The transport department knows your licence is up for renewal, any applicable background checks are completed and, if you are eligible for a renewal, your replacement licence is sent. The process has been automated.
Optimize – This is fancy!
The future lies in completing the stepped processes (digitize, digitalize, automate) to reach a steady state, and then applying machine learning to optimize the underlying processes.
To speed up the issue of your new licence, an algorithm monitoring the automated process will ‘smooth’ demand by adjusting the process to limit volume peaks and trigger early renewals.
In my job, too, more and more processes are being digitalised. We at Heidelberg Materials have already made some progress in this learning process. We have become more digital and are expanding our skill sets. Even just a few years ago, I wouldn't have imagined that by 2020 many of us would be using Office 365 and no longer have a landline phone, that our customers would be able to track concrete deliveries by smartphone using the OnSite app or that our aggregates inventories would be automatically updated with data from plant control via the Industrial Internet of Things. As you can see, we are constantly improving our processes, and we are well-prepared for a digital future.
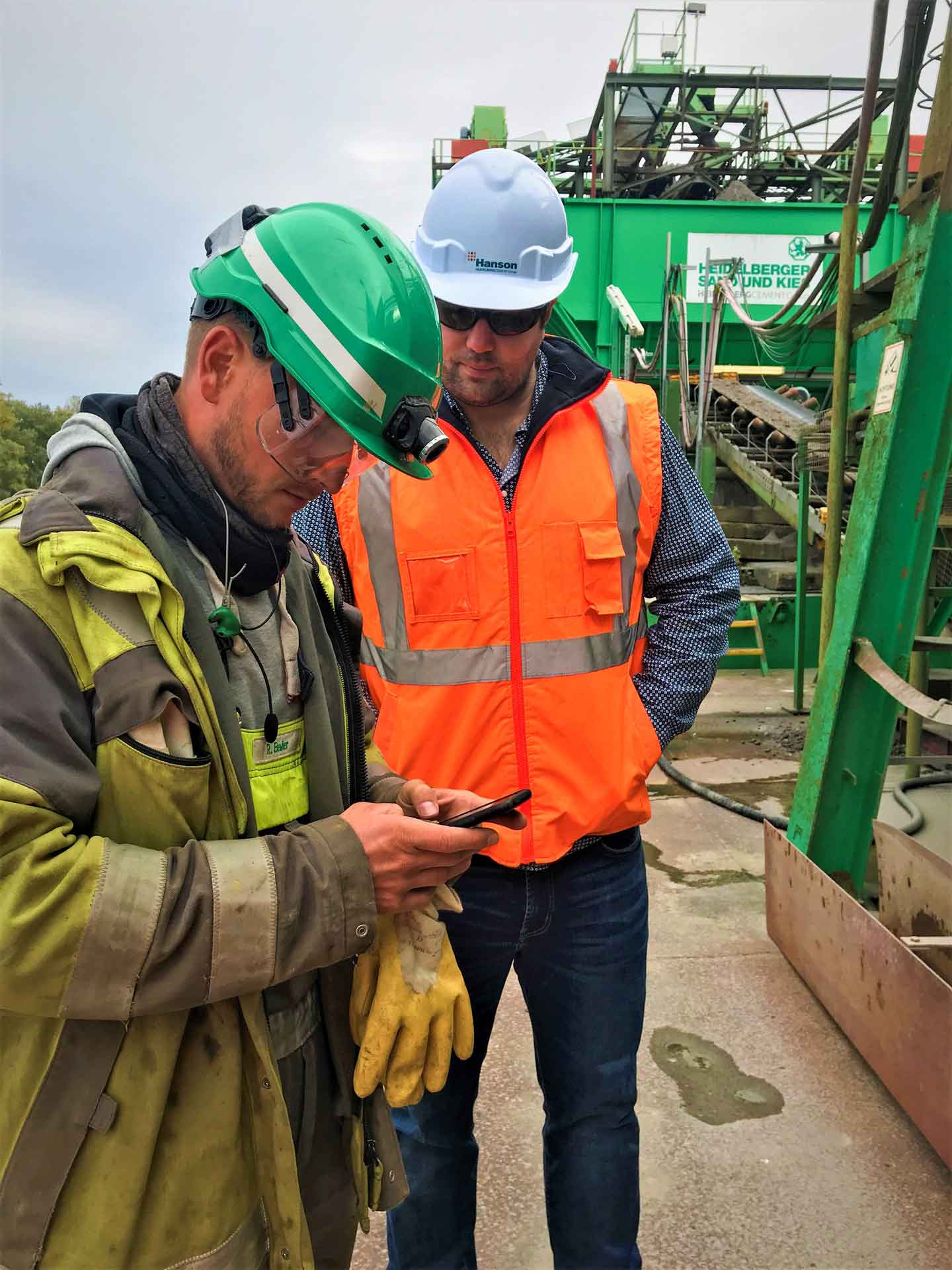
App in action.
Heidelberg Materials
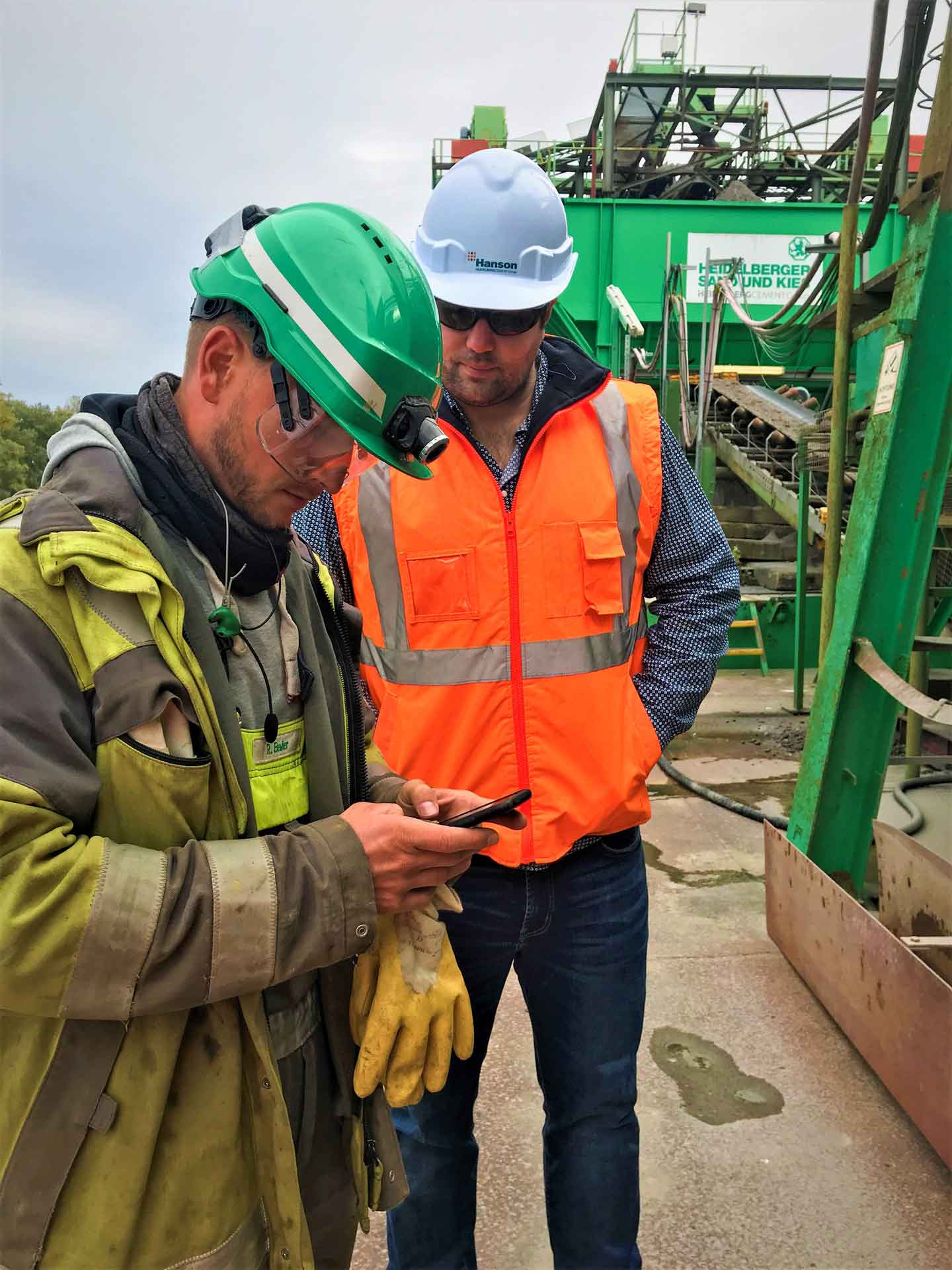
App in action.
Heidelberg Materials