Less non-recyclable plastics in Tanzania
Heidelberg Materials joins forces with start-up Cleanhub
Dar es Salaam, Africa’s third fastest-growing city, generates a lot of waste every day. Heidelberg Materials and Cleanhub join forces to take care of non-recyclable plastics and co-processing them in cement production.
Around 4,500 tonnes of waste are generated every day in Dar es Salaam. Only 40% of this waste is managed and mainly being landfilled at the local dumpsite. The remaining 60% is either burned or illegally dumped into rivers or the ocean causing a variety of health, economic and social related consequences.
Less non-recyclable plastics with Cleanhub
Cleanhub enables the recovery of plastic waste from the natural environment in emerging countries and links them with off-takers creating sustainable and profitable solutions for non-recyclable plastic waste. Full transparency and adherence with the highest social and environmental standards are ensured by Cleanhub’s tracking app, which keeps account of the person, quantity, quality and location for all plastic that is recovered. Working with Cleanhub, we can put a value on a non-recyclable plastic material that would otherwise have ended up in the waterways, burnt or at the landfill.
Every kilogram of plastic that goes through the Cleanhub project will mean one kilogram of waste taken out of the environment in Tanzania,
says Joel Tasche, co-founder at Cleanhub.
Together with our subsidiary Tanzania Portland Cement Public Limited Company (TPCP) – the largest cement producer in Tanzania, Cleanhub has found a sustainable solution for the use of non-recyclable plastic: co-processing in cement production.
How does co-processing work?
Co-processing non-recyclable plastics in the cement industry is a combination of material recycling and energy recovery, as ashes are being incorporated into the clinker. The materials can recover in an environmentally sound way in cement kilns. These kilns are readily available in emerging countries. No public investment in waste incineration is needed. It also leads to a reduction of CO₂ emissions by substituting coal, lignite and petcoke.
How can we make a difference with this project?
Over 300 million tons of plastic are produced every year. Only 9% of this plastic is being recycled, while 40% are being landfilled and 14% are being burned in waste incinerators. The rest is unaccounted leading to uncontrolled environmental pollution threatening food safety and quality and health. With co-pressing in local cement industries, we found a cost-efficient and environmentally safe solution for this challenge. When high scaling the practice and adding public support, co-processing in the cement industry can make a difference.
By teaming up with Cleanhub, TPCP can reduce costs while lowering the carbon footprint.,
says Alfonso Rodriguez, General Manager for Central and South-East Africa Operations.
With co-processing, we protect the environment and prevent uncontrolled pollution by putting a value on a non-recyclable plastic material that would otherwise have ended up in e.g. waterways or landfills. We are also providing new business opportunities for emerging societies by creating access to off-takers for non-recyclable plastics and by incentivizing and remunerating waste collection and waste management.
A clear win-win for all!,
says Alfonso Rodriguez.
Heidelberg Materials intends to extend the cooperation with Cleanhub to other emerging countries.
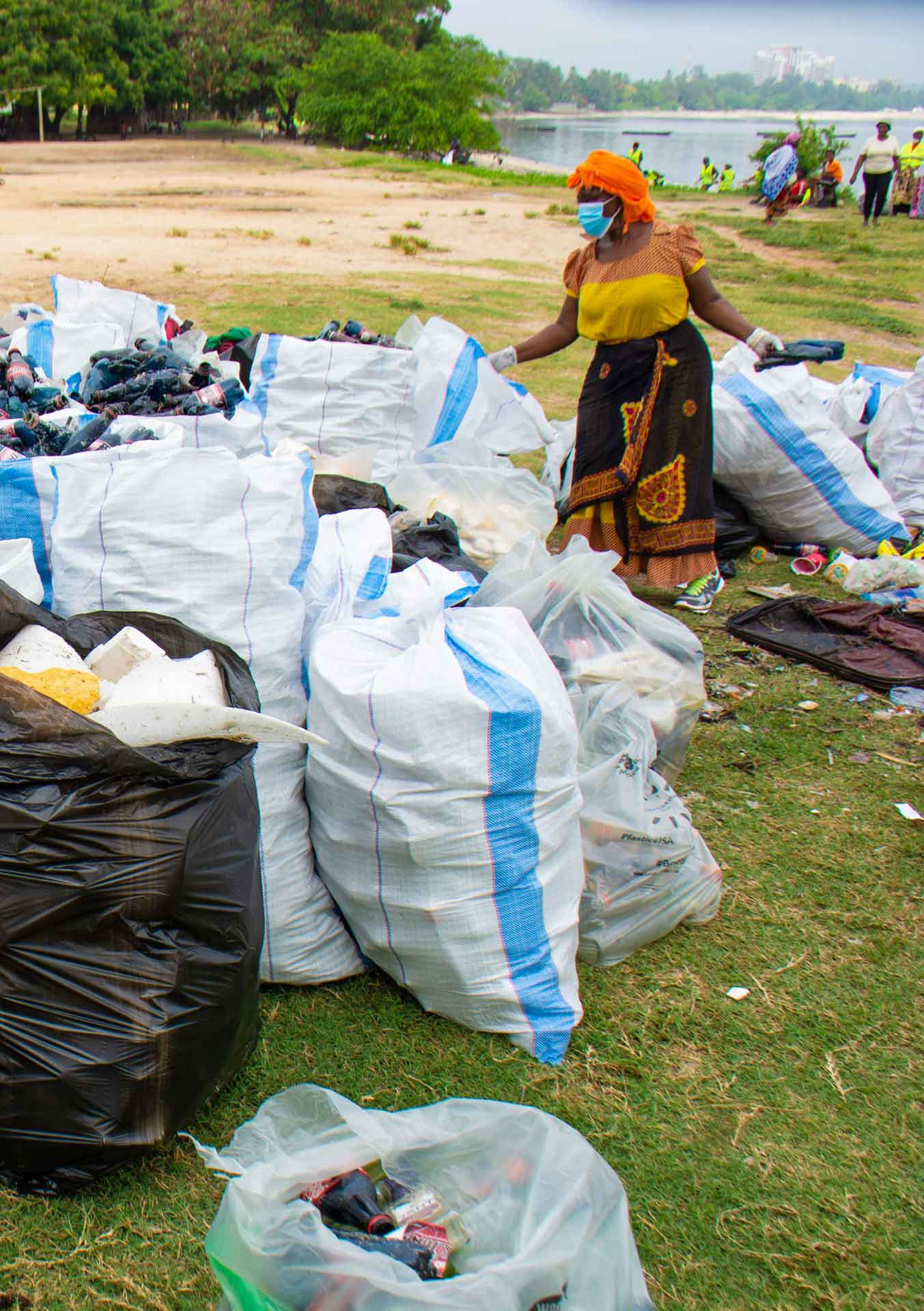
Collecting plastic waste in Tanzania.
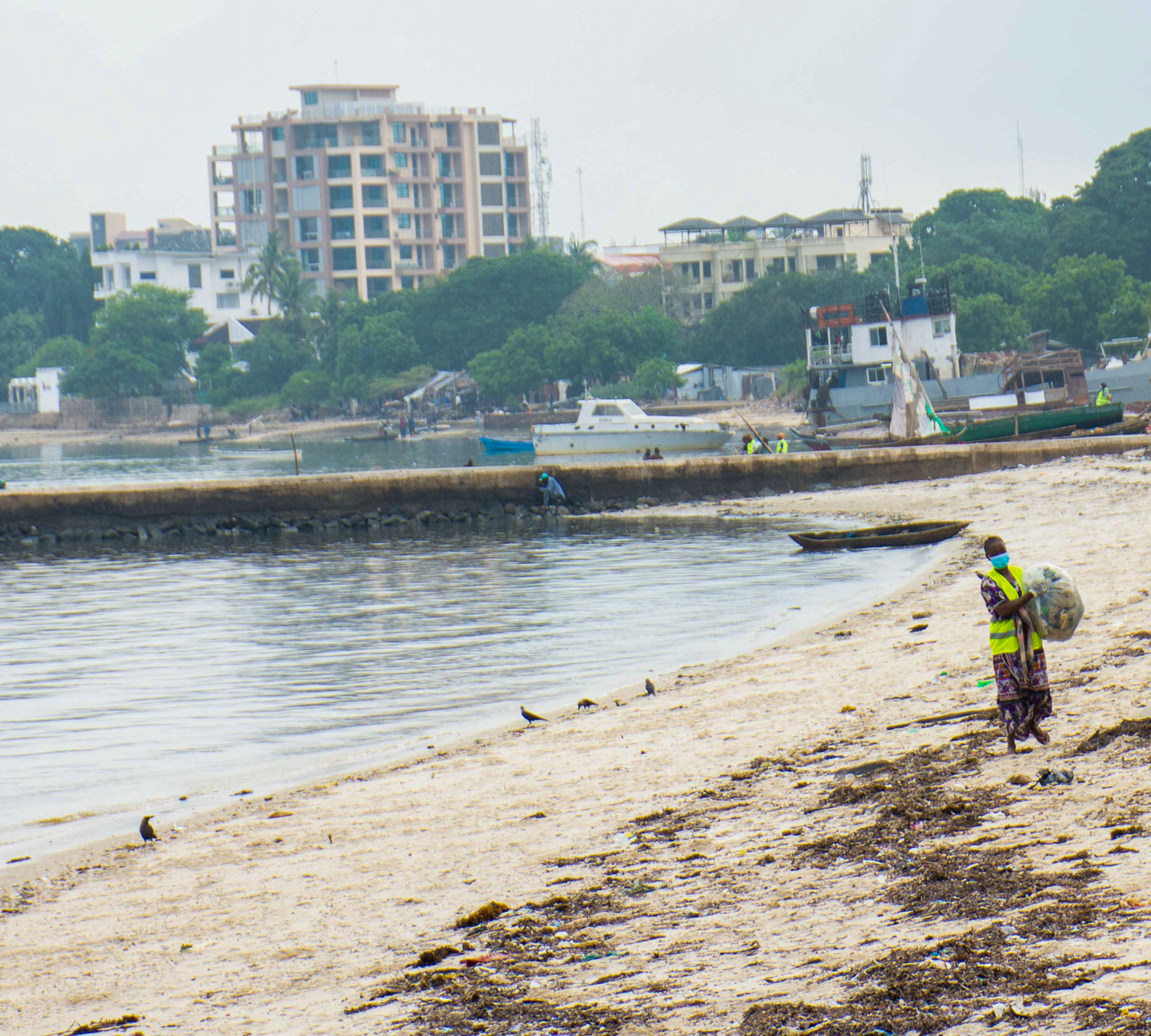
Cleaned up beach.
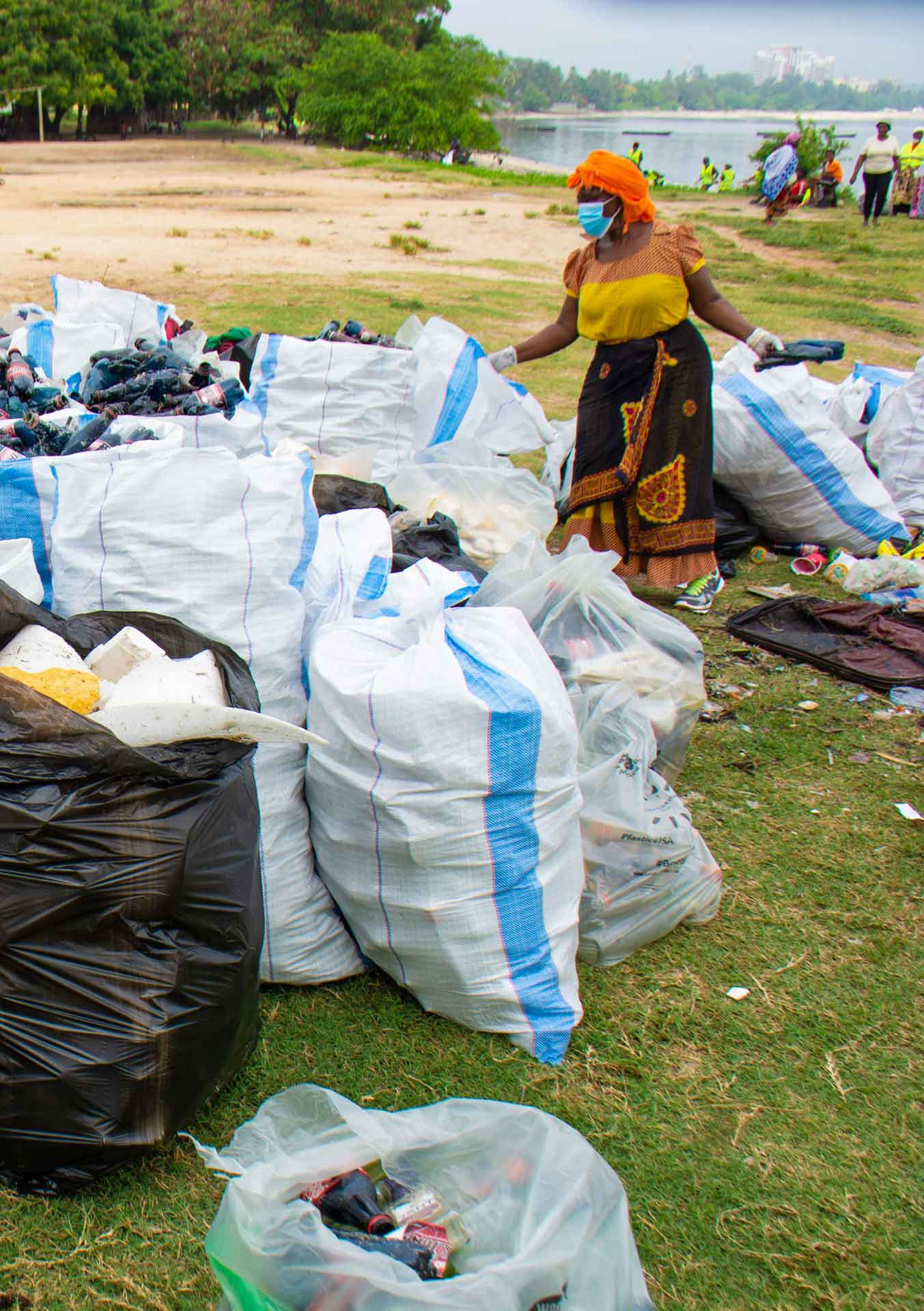
Collecting plastic waste in Tanzania.
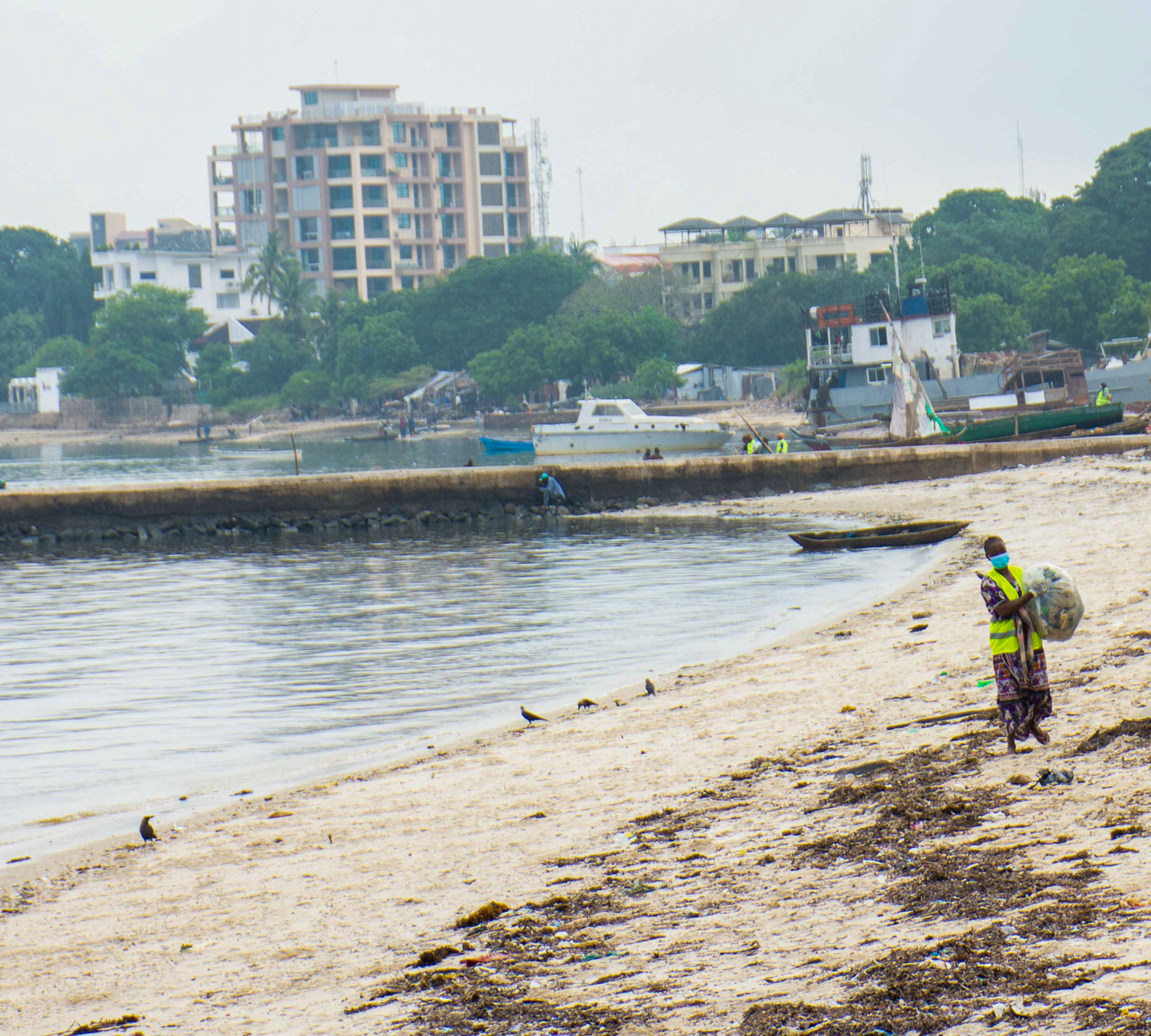
Cleaned up beach.