A new CCU approach
CO₂ mineralization of demolished concrete wastes
The concept relies on improved concrete recycling where the fines rich in cement paste are separated out from sand and coarser aggregate. These fines are then enforced carbonated, producing a new material that can be utilised in the production of new composite cements. When properly treated, carbonated recycled concrete paste (RCP) is characterized by similar properties as typical pozzolan, e.g. fly ash, in composite cements. The experience with the carbonation of recycled concrete and application of this material for the development of composite cements is summarized in a scientific publication
CO₂ mineralization of demolished concrete wastes into a supplementary cementitious material – a new CCU approach for the cement industry”.
Concrete paste as a CO₂ sink and a supplementary cementitious material
The fundamental concept of mineral carbonation is that the hydraulic cement components and their hydration products can readily react with the CO₂ in a humid environment. Most of the CO₂, originally released by limestone calcination during clinker production, can be sequestered by carbonation of the RCP. This carbonation can be achieved in the range between several minutes and a few hours at ambient temperature and pressure.
A relatively low CO₂ concentration in the gas can be used, for example corresponding to the exhaust gases from the cement plant. The carbonation of cement paste produces calcium carbonate and an amorphous gel, the latter being a pozzolanic material. The pozzolanic reaction of the gel is very rapid resulting in the formation of compressive strength. The material can therefore be utilised as a supplementary cementitious material allowing the reduction of the cement clinker content in the cement.
Circular economy with recarbonation
The application of the RCP for cement production has two principal advantages: it allows for CO₂ sequestration during the carbonation process and it can be used in composite cements, thereby further reducing CO₂ emissions of cement production. The concept contributes to the circular economy and preserves natural resources as all materials derived from demolished concrete can be recycled and used in new concrete production. Therefore, it is an inherent part of Heidelberg Materials' way to carbon neutrality.
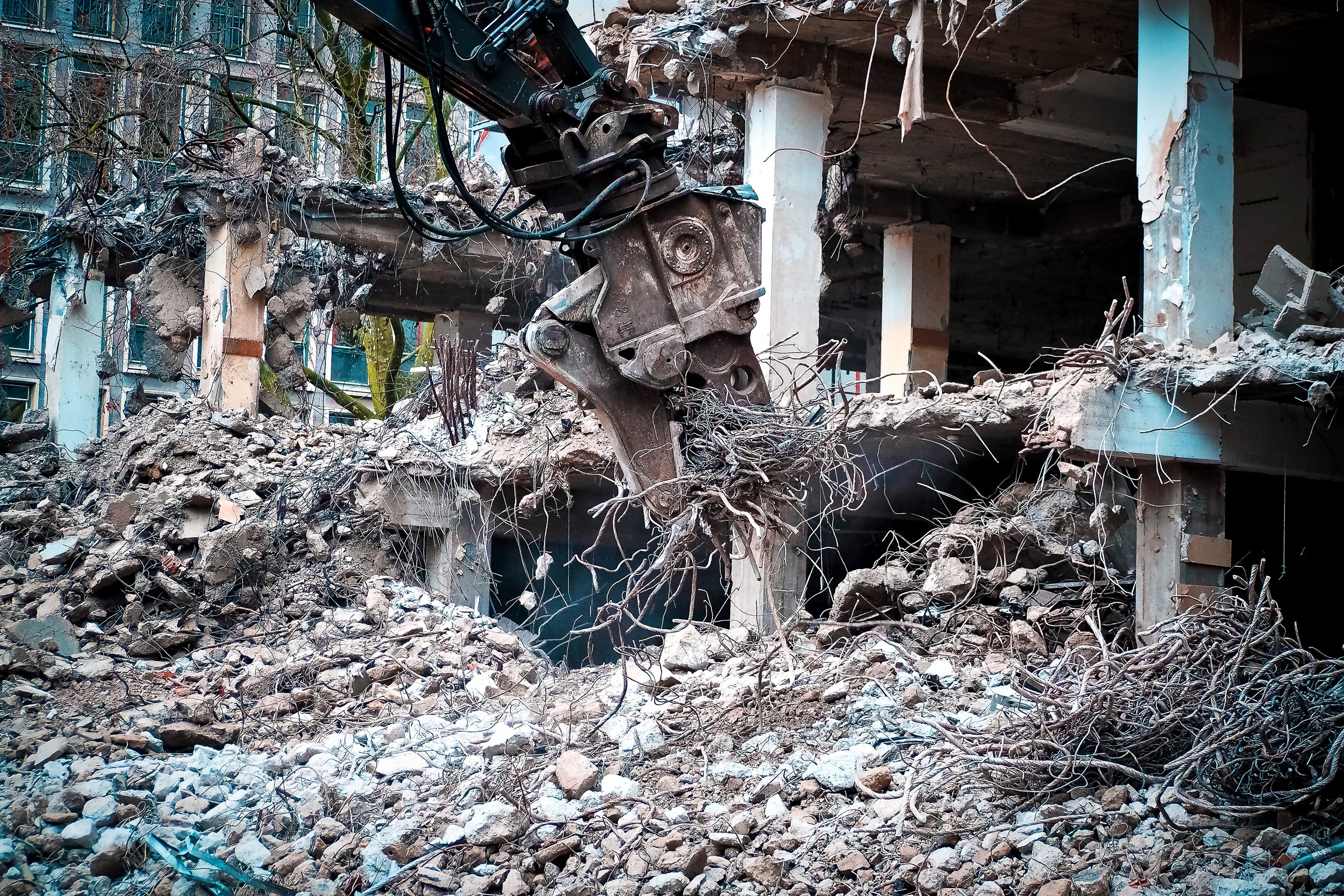
Concrete demolition.
Michael Gaida/Pixabay
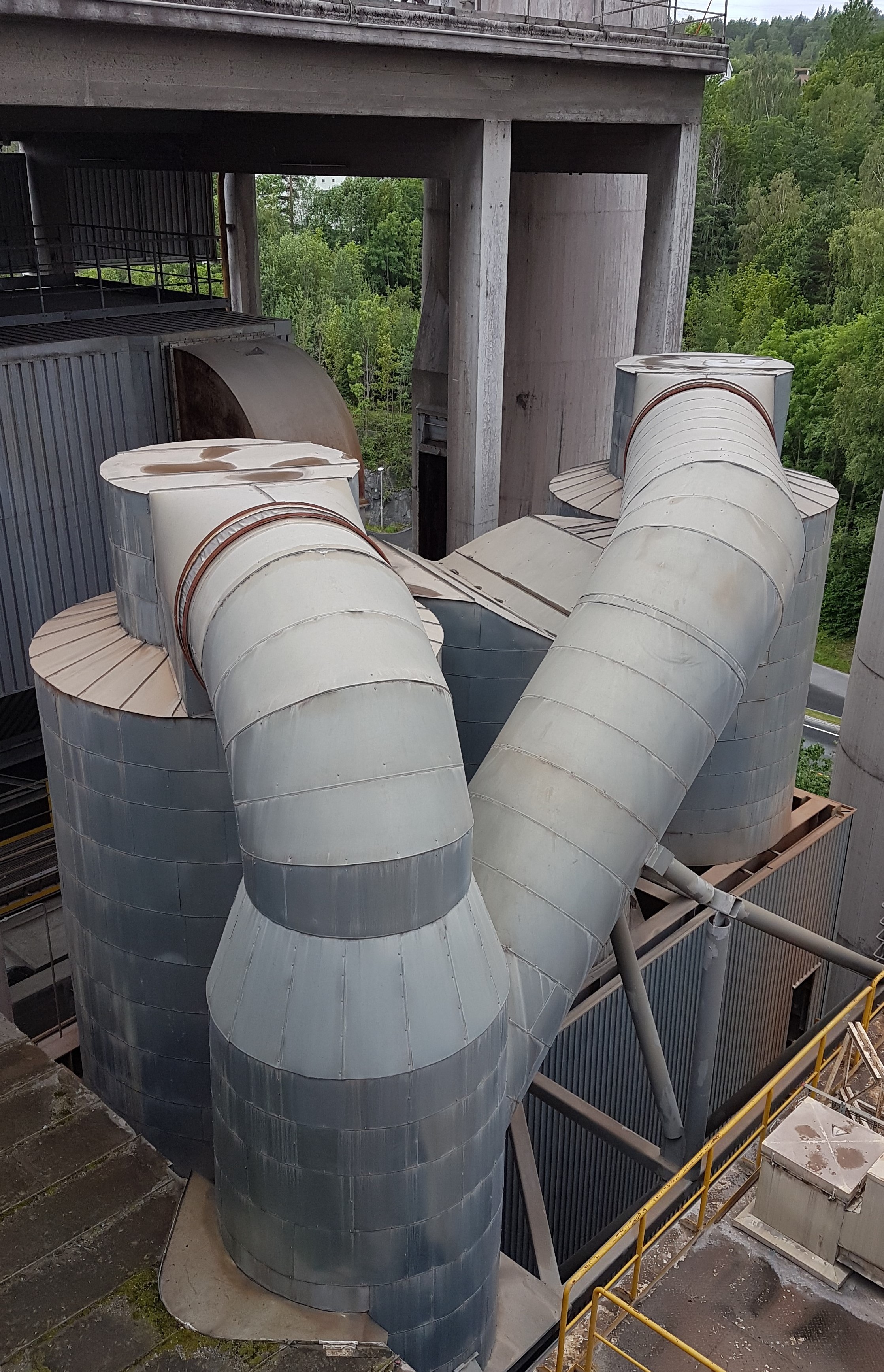
CFB absorber used in Brevik to capture CO₂ from the kiln stack using recycled concrete as a sequestration substrate.
Heidelberg Materials
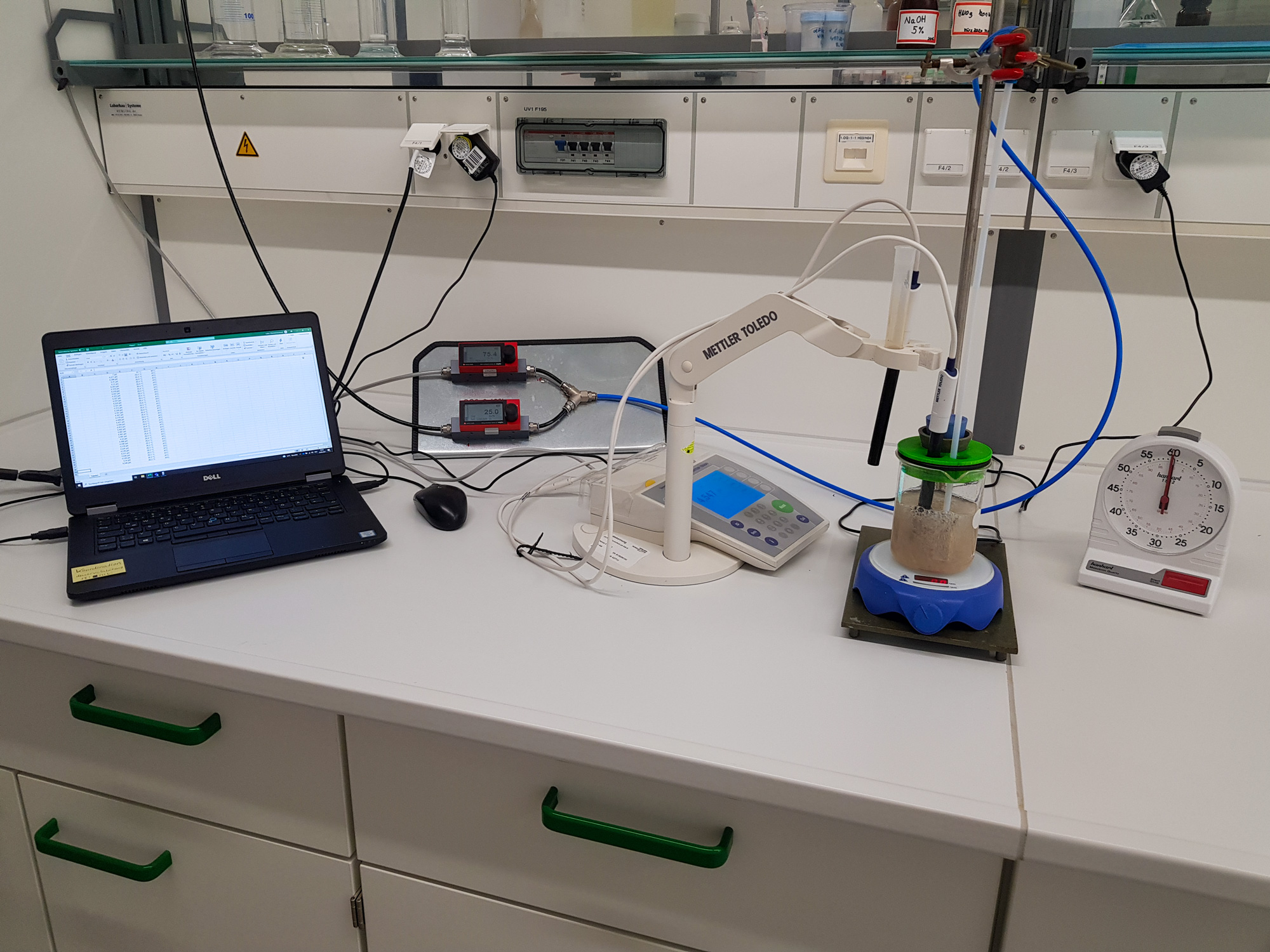
In the lab.
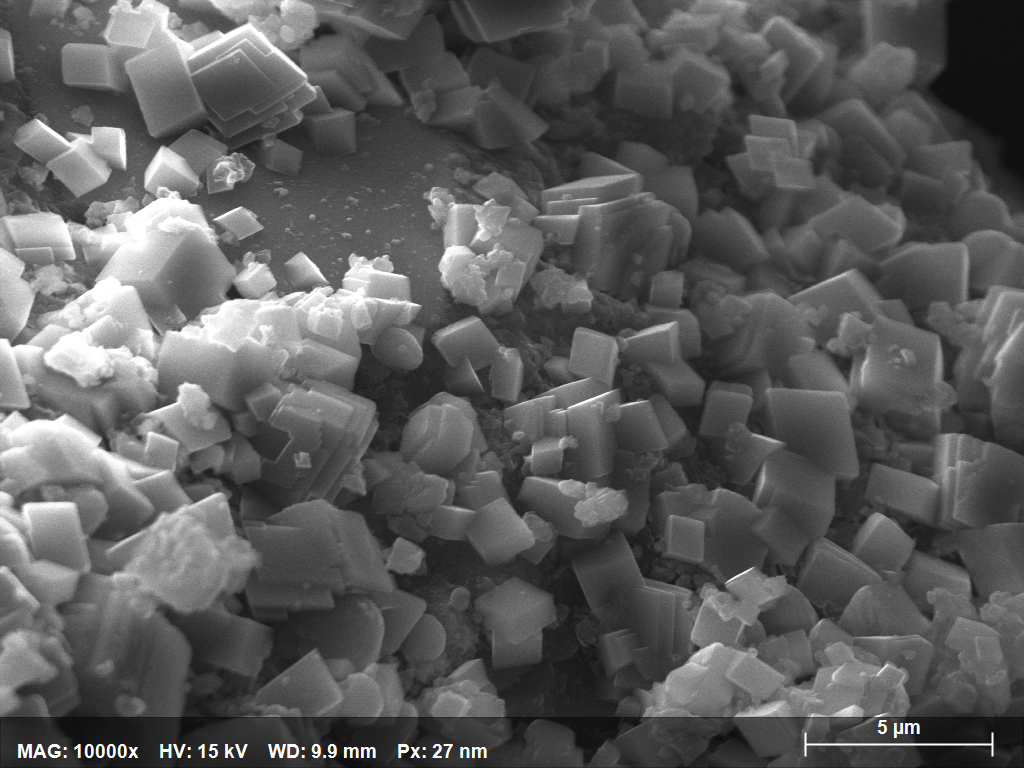
Scanning electron microscope image showing the morphology of the calcium carbonate.
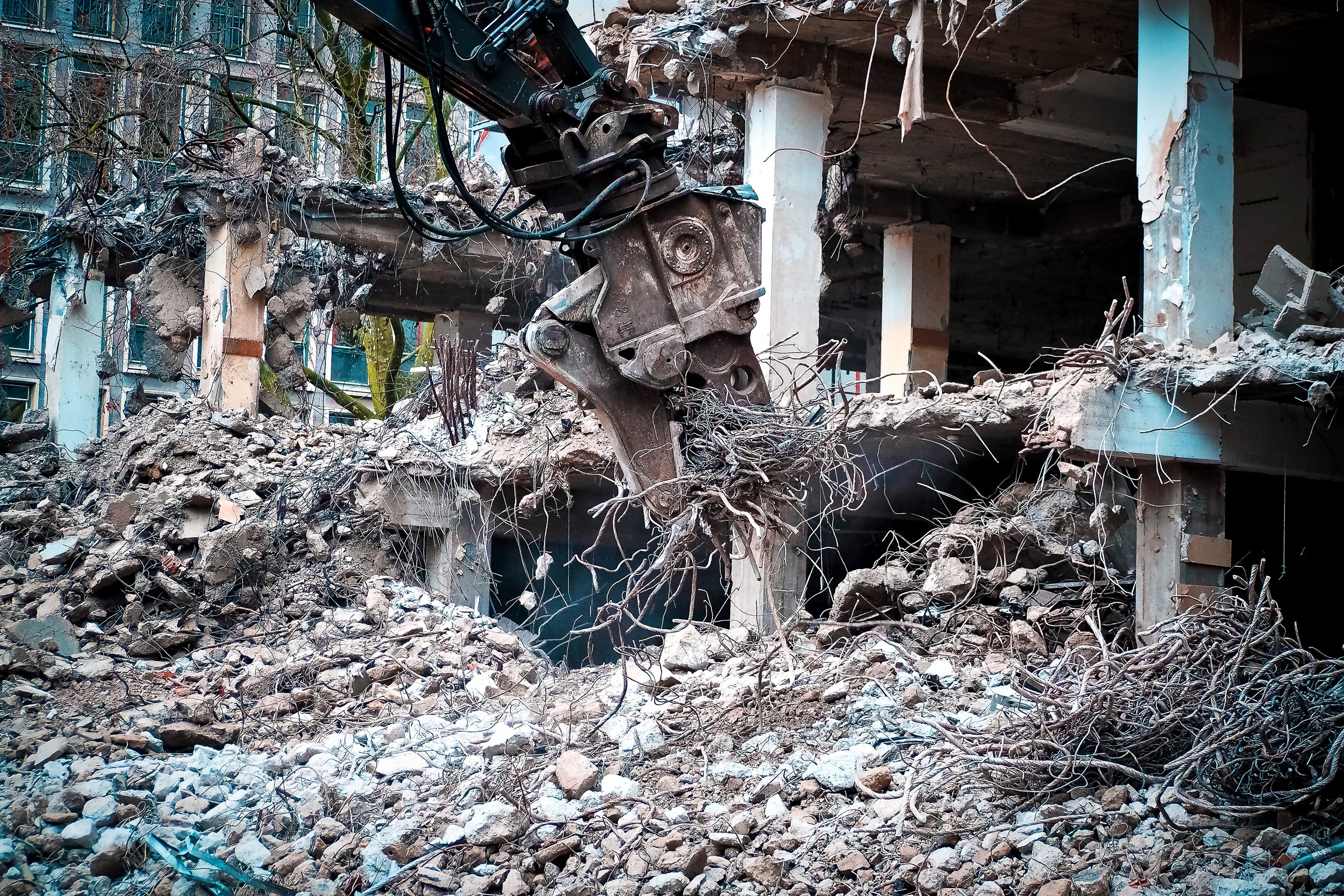
Concrete demolition.
Michael Gaida/Pixabay
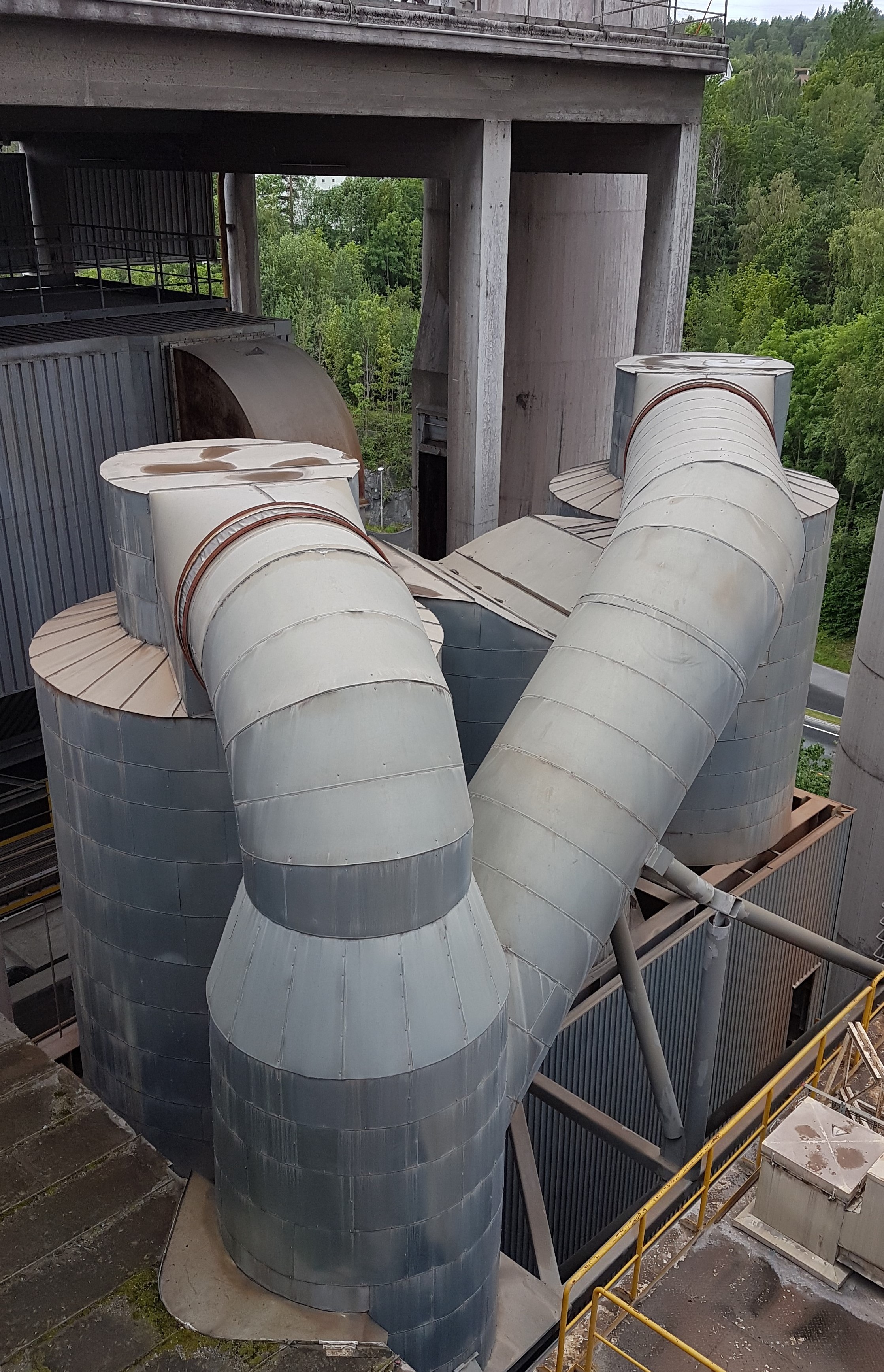
CFB absorber used in Brevik to capture CO₂ from the kiln stack using recycled concrete as a sequestration substrate.
Heidelberg Materials
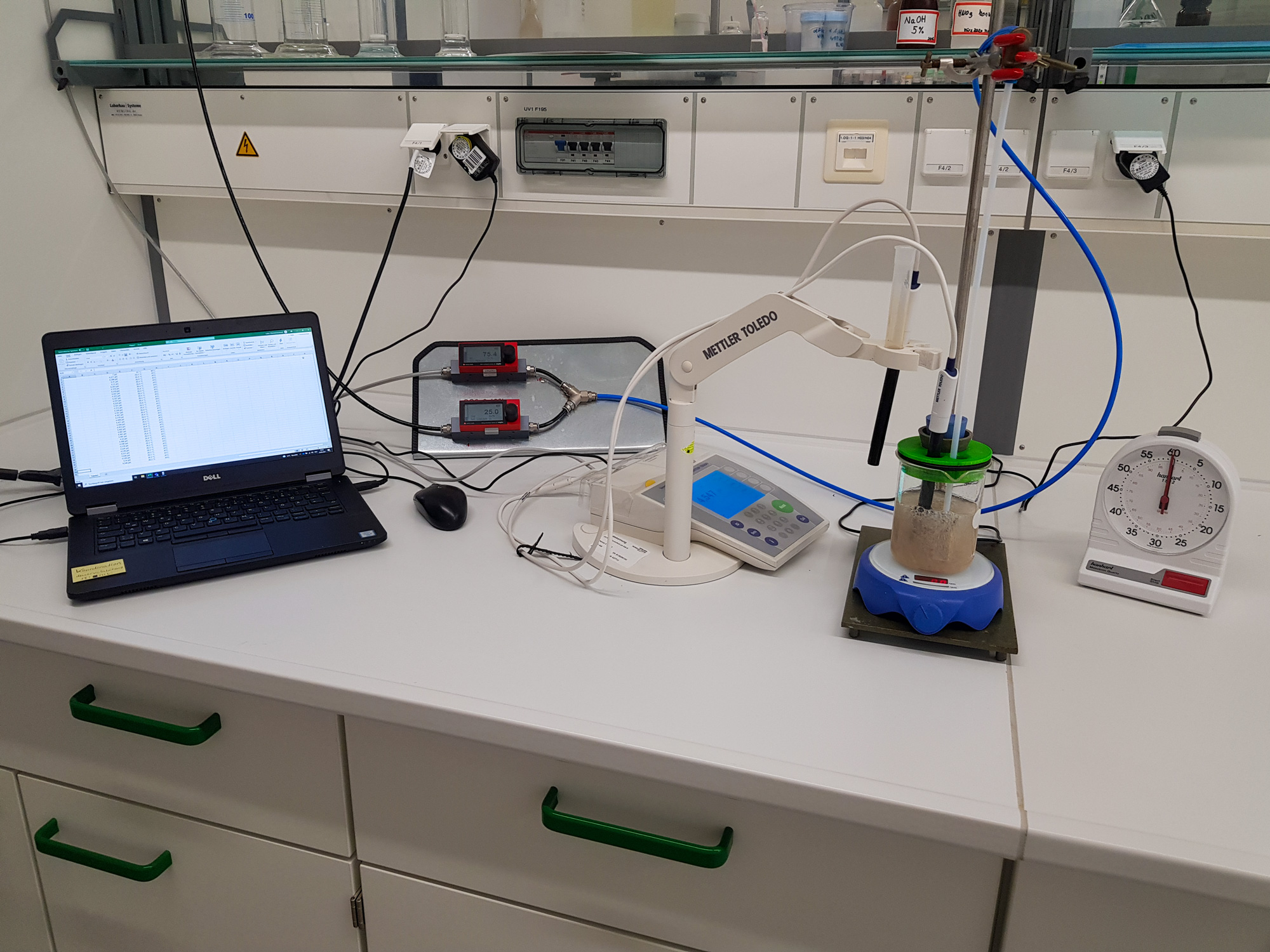
In the lab.
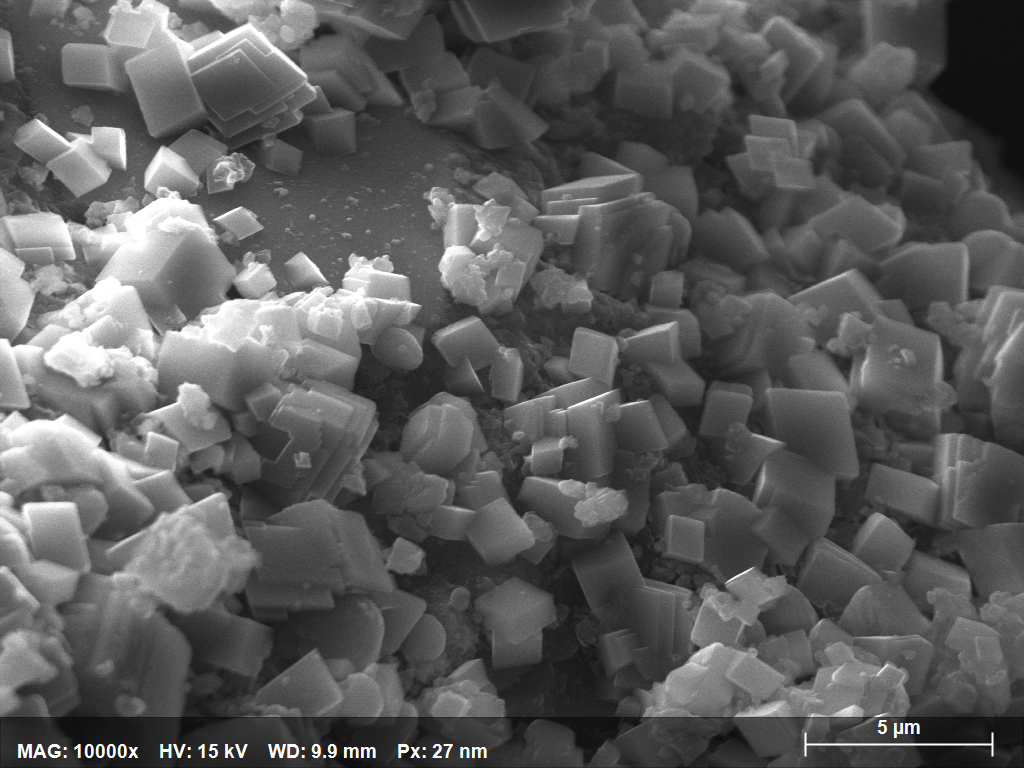
Scanning electron microscope image showing the morphology of the calcium carbonate.